Throttle Quadrants
We tailor the design and testing of our throttle quadrants to suit each unique application. Over the years, we've provided custom aircraft throttle quadrants for a wide range of aircraft, including commuter aircraft, executive aircraft, helicopters, and specialized applications such as the US Navy PHM, Boeing Jet Foil, US Navy LCAC, and USMC LVTP-7 gear section quadrant.
tailored with precision
Our aircraft throttle quadrants are tailored with precision for any aircraft application.
Ergonomics
- Knob size (shape fairly standard per FARs)
- Go-around switch location
- Friction (wheel, lever, or constant, materials)
- Detent type (lift buttons/knobs, lift lever, push to side) to side)
- Power/condition lever length
- Reverse method ((T/R or reverse ppp)rop.)
- Visual position indicators (engraving, edge-lighted panel – NVG compatible)
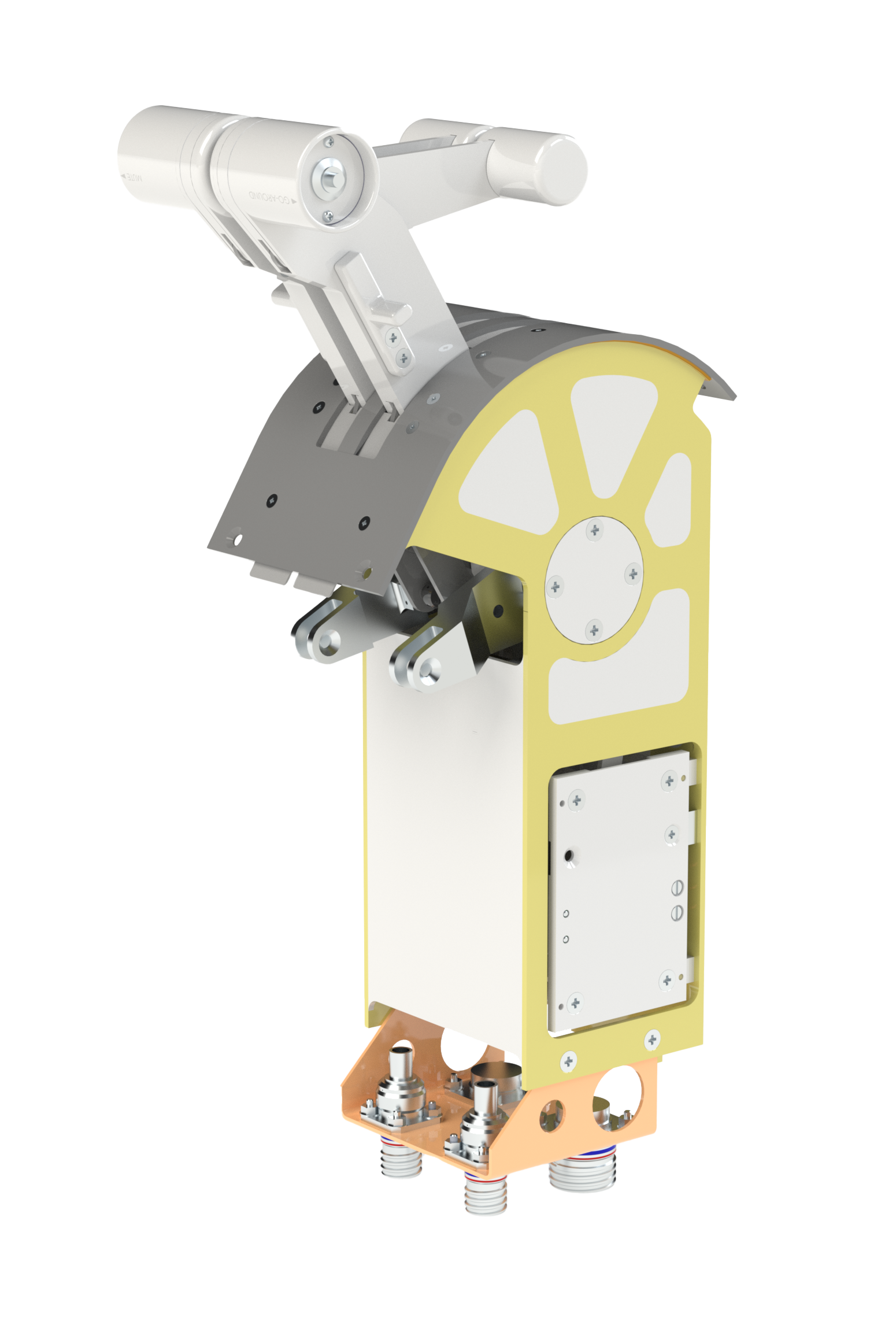
Durability
- Housing (typically rubber mold casting) strength to provide mounting/load path for all components
- Levers (machined, square tube)
- Knob material properties (Typically composite Molded or Knob material properties (Typically composite. Molded or machined. Good thermal properties, degradation resistant, Material strength for mounting inserts and constant use)
- Switch selection criteria (cycles rating contact type) Switch selection criteria cycles, rating, contact type)
- Switch bank actuation mechanism
- RVDT/Potentiometer life
- Friction material life
Output
- Mechanical through clevis to push-pull rods or cables (must maximize mechanical advantage and minimize system friction)
- Electro-mechanical (switch banks for discreet position signals, not FBW) through rods, cables and connectors
- FBW w/ Mechanical Back-up (must synchronize) mechanical output and electronic signal)
- FBW – Potentiometers, RVDTs. (Must consider Potentiometers, RVDTs. (Must consider tolerances, application, redundancy)
Reliability & Maintainability
- Past design experience used to meet customer specifications.
- MTBF, MTBUR MTBUR
- Met by choice of materials, switches and design/interface of dynamic components
- Plug & Play TQA for easy installation/rigging/removal
- Optimize on previous design experience Optimize on previous design experience
- Modular assembly
- Minimize need for special tools
- ATP equipment specific to product
Weight
- Always a balance between operational requirements functional requirements and requirements, functional requirements and environmental requirements
- Goal is maximum strength minimum weight Goal is maximum strength, minimum weight
- Some flexibility with castings (style, wall-thickness) and materials
Environmental Considerations
- Military (stringent for operational exposure)
- Commercial (stringent for dispatch rate)
- General Aviation (stringent for dispatch rate)
- Helicopter (vibration)
- Installation location
- Protected cockpit Protected cockpit
- Will not be used as a step?
Throttle Quadrant Benefits/Applications
Mechanical
In our mechanical throttle quadrants, precision engineering meets robust construction to provide tactile control and responsiveness for critical flight applications, ensuring safety and performance.
Electro-mechanical
Our electro-mechanical throttle quadrants seamlessly integrate electronic precision with mechanical reliability, offering advanced fly-by-wire control systems to meet the most demanding aviation requirements.
FBW with Mechanical Back-up
Our FBW (Fly-By-Wire) with mechanical back-up throttle quadrants combine cutting-edge electronic control with robust mechanical systems, ensuring aircraft safety and performance even in emergency situations.
Completely FBW
Our completely FBW (Fly-By-Wire) throttle quadrants represent the pinnacle of modern aircraft control, providing precise, reliable, and highly responsive performance, enhancing the flight experience and pilot confidence.